Advanced Techniques in Metal Stamping for Accuracy Production
As markets consistently demand finer resistances and detailed designs in their steel parts, the quest for sophisticated strategies in steel stamping has actually intensified. From the use of innovative multi-stage marking processes to the combination of innovative automation modern technologies, the landscape of metal stamping is going through an extensive makeover.
Advanced Multi-Stage Stamping Processes
Talking about the ins and outs of innovative multi-stage marking procedures exposes the sophisticated methods employed in modern production methods. Metal Stamping. Multi-stage stamping is an intricate procedure that involves multiple steps to transform a flat sheet of metal into a final stamped product. Using modern dies, where different operations are done at each stage of the stamping process, permits high precision and effectiveness in the manufacturing of detailed steel components
Throughout the preliminary stages of multi-stage stamping, the flat steel sheet is fed right into the marking press, where a collection of dies are used to cut and shape the product. Succeeding phases include extra forming, bending, and punching procedures to more improve the component. Each stage is very carefully created to build on the previous one, causing the development of complicated geometries with tight tolerances.
Advanced multi-stage marking procedures call for a high degree of know-how and accuracy to guarantee the high quality and consistency of the stamped parts. By utilizing sophisticated equipment and tooling, suppliers can create a vast array of metal parts with efficiency and precision.
Accuracy Tooling Innovations
Accuracy tooling advancements have actually transformed the metal marking market, boosting performance and quality in making procedures. These developments have considerably affected the method steel elements are created, causing greater accuracy and uniformity in the end products. One essential development is the advancement of computer system mathematical control (CNC) innovation in tooling design and fabrication. CNC systems permit complex styles to be converted directly right into tooling, guaranteeing accuracy and repeatability in the marking procedure.
Furthermore, the combination of sensors and real-time monitoring abilities in accuracy tooling has actually made it possible for manufacturers to discover and attend to problems immediately, decreasing downtime and lowering scrap prices. By including clever modern technology right into tooling, drivers can maximize specifications such as stress, speed, and positioning during the stamping operation, causing boosted item high quality and boosted efficiency.
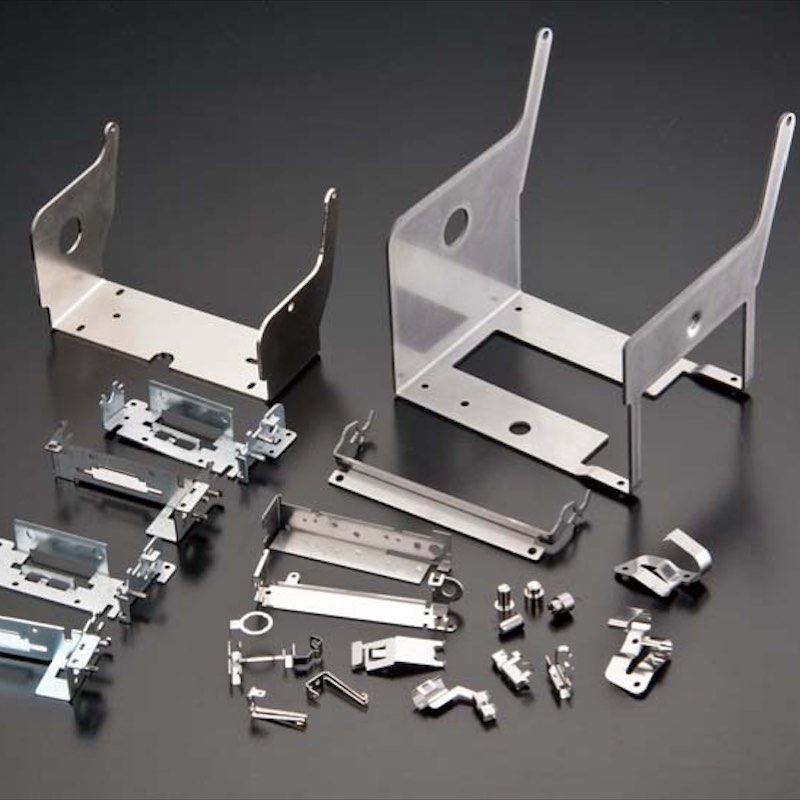
Automation in Steel Stamping
The development of precision tooling developments in the metal stamping sector has actually led the method for considerable developments in automation, transforming the production landscape in the direction of boosted effectiveness and productivity. Metal Stamping. Automation in metal marking includes the use of sophisticated equipment and robotics to do different tasks commonly lugged out by human operators. This shift in the direction of automation uses various benefits, consisting of enhanced accuracy, faster manufacturing cycles, and minimized labor expenses
One key facet of automation in steel stamping is the application of computer system numerical control (CNC) systems, which Resources make it possible for specific control over the marking process. CNC modern technology permits the development of complex and complex metal get rid of constant top quality. Furthermore, automated systems can be programmed to run constantly, resulting in greater output prices and shorter preparations.
Furthermore, automation boosts workplace safety and security by decreasing hand-operated handling of heavy products and reducing the danger of accidents (Metal Stamping). As producing sectors remain to welcome automation, the future of steel stamping holds wonderful guarantee for also greater effectiveness and technology
High-Speed Stamping Techniques
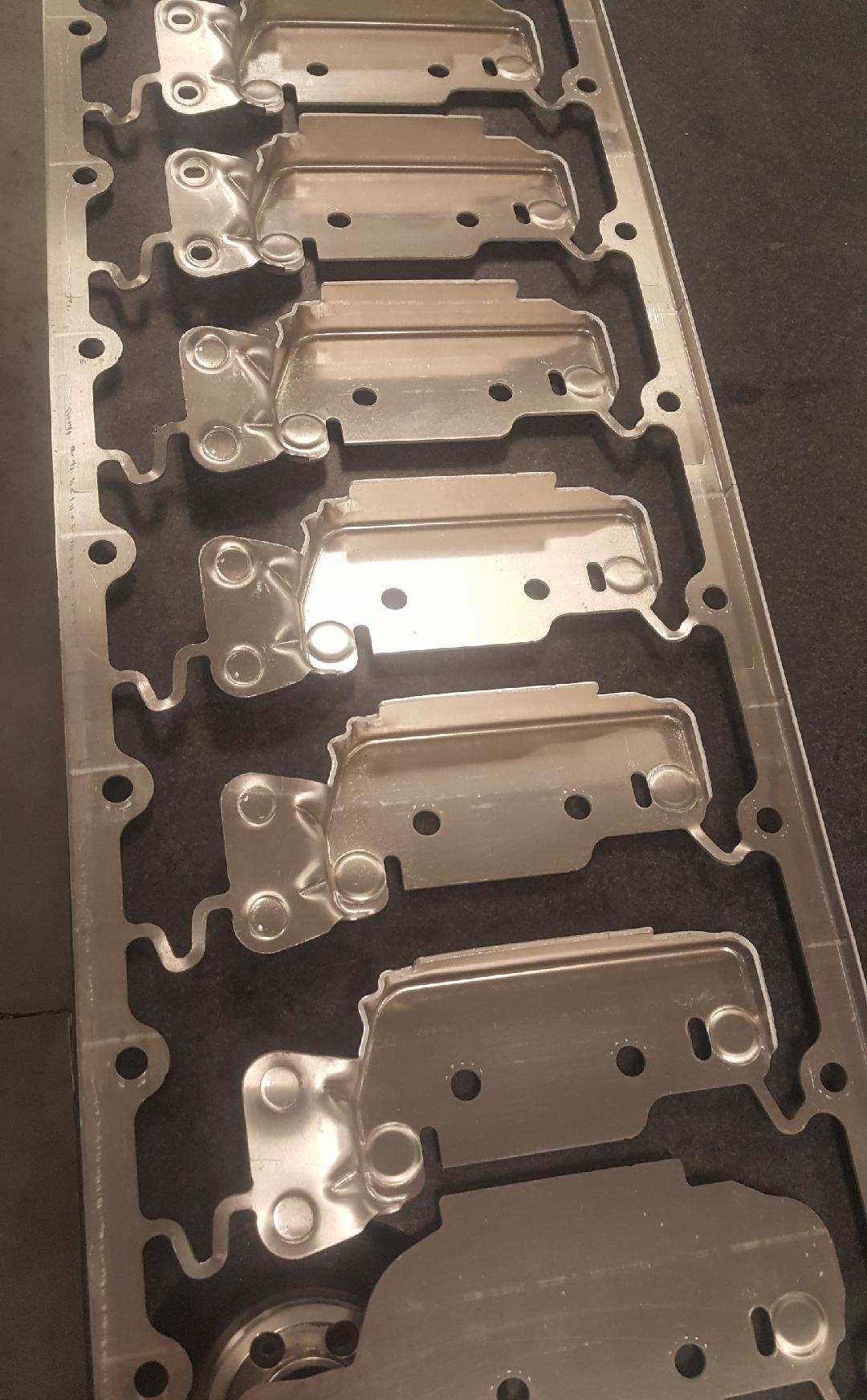
Among the key benefits of high-speed marking techniques is the ability to produce a large volume of parts in a shorter amount of time compared to conventional stamping techniques. This boosted performance not just permits suppliers to fulfill limited manufacturing target dates yet additionally makes it possible for price financial savings with economic climates of range. Furthermore, high-speed marking can help in reducing material waste by enhancing the product use during the marking process.
Furthermore, high-speed marking methods typically include cutting-edge attributes such as fast die adjustment systems and real-time surveillance abilities, even more enhancing the overall performance and adaptability of the steel stamping procedure. As modern technology proceeds to breakthrough, high-speed marking is anticipated to play an essential role in driving the future of precision production.
High Quality Control in Stamping Procedures
Efficient quality assurance steps are important for ensuring the integrity and consistency of metal marking operations. Quality assurance in stamping operations entails a series of organized procedures targeted at detecting and protecting against problems in the made parts. One vital aspect of quality control in metal click now marking is making use of advanced evaluation strategies such as optical inspection systems and coordinate measuring devices (CMMs) to validate the measurements and tolerances of stamped components.
Furthermore, high quality control actions in marking operations frequently consist of the implementation of analytical procedure control (copyright) techniques to check the production procedure in real-time and ensure that it stays within appropriate limits. By evaluating information and identifying patterns, suppliers can proactively address any type of inconsistencies from the desired high quality criteria.
Furthermore, top quality control in metal stamping procedures additionally involves extensive product screening to ensure that the raw materials utilized satisfy the called for requirements for the stamping process. This might include conducting material firmness tests, tensile toughness examinations, and dimensional evaluations to ensure the high quality and honesty of the stamped parts. On the whole, implementing robust quality assurance steps is vital for accomplishing high-grade stamped components continually.
Verdict
To conclude, progressed strategies in steel marking play a critical duty in accuracy production processes. With multi-stage stamping processes, cutting-edge tooling remedies, automation, high-speed methods, and rigorous quality assurance measures, manufacturers can attain greater levels of accuracy and efficiency in their procedures. These innovations in steel stamping technology have actually made it possible for business to create complex components with limited tolerances, ultimately bring about enhanced product quality and consumer fulfillment in the manufacturing sector.
Comments on “Leading Metal Stamping Solutions for High-Quality and Cost-Effective Manufacturing”